Excavators are indispensable in the construction and mining industries, performing crucial tasks such as digging, trenching, and material handling. Given their significant role, ensuring that these machines operate at peak efficiency is vital. Efficient excavator operations lead to increased productivity, reduced operational costs, and prolonged equipment lifespan. This blog will provide you with essential tips to improve excavator efficiency, covering various aspects such as maintenance, operator training, proper use of attachments, advanced digging techniques, technology integration, fuel management, tire and track maintenance, and job site management. By following these tips, you can enhance the performance of your excavator, reduce downtime, and maximize profitability.
1.Regular Maintenance
Regular maintenance is the cornerstone of improving excavator efficiency. By ensuring that your machine is in optimal condition, you can prevent unexpected breakdowns, extend its lifespan, and enhance overall performance. Here’s a detailed look at key maintenance practices:
Routine Inspections
Conducting routine inspections is essential for identifying potential issues before they become major problems. Daily checks should include:
Visual Inspection: Walk around the excavator and look for any visible signs of damage or wear, such as leaks, cracks, or loose parts.
Hydraulic System Check: Inspect hydraulic hoses and connections for leaks or signs of wear. Ensure that the hydraulic fluid level is adequate and that the fluid itself is clean.
Engine Inspection: Check the engine for any signs of oil leaks or damage. Ensure that belts and hoses are in good condition and properly tensioned.
Routine inspections help in early detection of issues, allowing for timely intervention and minimizing costly downtime.
Checking Fluids and Filters
Maintaining proper fluid levels and ensuring clean filters are crucial for the smooth operation of an excavator. Key areas to focus on include:
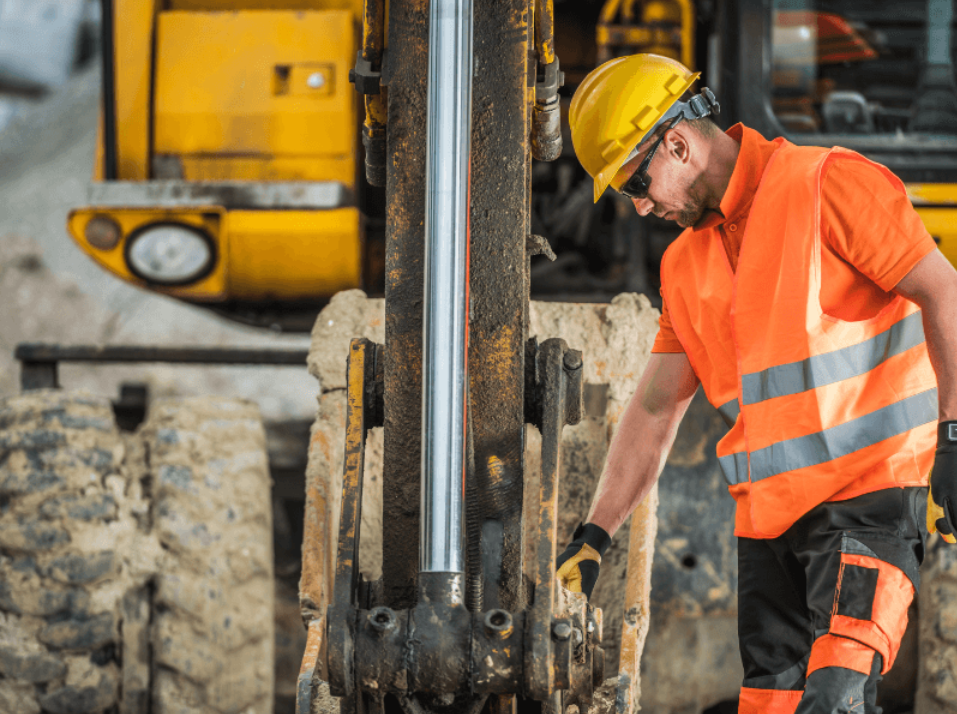
Hydraulic Fluid: Regularly check and top up the hydraulic fluid. Contaminated or low hydraulic fluid can lead to poor performance and damage to the hydraulic system.
Engine Oil: Monitor engine oil levels and change the oil according to the manufacturer’s recommendations. Clean oil ensures that the engine runs smoothly and reduces wear and tear.
Coolant: Ensure that the coolant level is sufficient to prevent the engine from overheating. Use the recommended type of coolant to avoid corrosion and other issues.
Air and Fuel Filters: Replace air and fuel filters regularly to maintain optimal engine performance. Clogged filters can restrict airflow or fuel supply, leading to reduced efficiency and potential engine damage.
By keeping fluids at appropriate levels and using clean filters, you ensure that the excavator operates efficiently and reliably.
Importance of Timely Repairs
Addressing mechanical issues promptly is critical for maintaining excavator efficiency. Delaying repairs can lead to more severe damage and increased repair costs. Key considerations include:
Preventive Maintenance: Implement a preventive maintenance schedule to address potential issues before they lead to breakdowns. This includes regular servicing as per the manufacturer’s guidelines.
Early Detection and Action: Act on any warning signs such as unusual noises, vibrations, or performance drops. Early detection and repair of issues can prevent major failures.
Using Genuine Parts: When repairs are needed, use genuine parts from the manufacturer. They are specifically designed for your excavator model and ensure optimal performance and longevity.
Timely repairs minimize downtime and keep your excavator running efficiently, ultimately saving you time and money.
By prioritizing routine inspections, maintaining proper fluid levels and clean filters, and addressing repairs promptly, you can significantly enhance the efficiency and lifespan of your excavator. Regular maintenance is an investment in reliability and productivity, ensuring your machine performs at its best in every task.
Operator Training
A well-trained operator is crucial for maximizing excavator efficiency. Skilled operators not only perform tasks more quickly and accurately but also ensure the machine is used properly, reducing wear and tear. Investing in operator training can significantly impact your overall productivity and cost-effectiveness. Here’s how:
Skills and Knowledge Required
Operators need a specific set of skills and knowledge to handle excavators efficiently and safely. Key areas include:
Machine Operation: Understanding the controls, functions, and capabilities of the excavator. This includes knowing how to operate different attachments and utilizing them appropriately for various tasks.
Safety Protocols: Being aware of safety procedures to prevent accidents and injuries. This involves knowledge of site safety rules, proper use of personal protective equipment (PPE), and emergency response practices.
Basic Maintenance: Knowing how to perform basic maintenance tasks such as checking fluid levels, inspecting hydraulic systems, and identifying potential issues early. This ensures the machine remains in good working condition.
Problem-Solving Skills: Ability to troubleshoot common problems that may arise during operation. This includes recognizing symptoms of mechanical issues and taking appropriate actions to address them.
Having a strong foundation in these areas enables operators to work more efficiently and minimize downtime due to operational errors or safety incidents.
Regular Training Sessions
Continuous education is vital to keep operators updated on the latest techniques and technological advancements. Implementing regular training sessions can include:
Initial Training: Comprehensive training for new operators to ensure they understand the basics of excavator operation and safety.
Ongoing Training: Periodic training sessions to reinforce existing knowledge and introduce new practices. This can include refresher courses and advanced training for experienced operators.
Technology Updates: Training on new technologies and software that can enhance excavator performance. This includes familiarization with GPS systems, telematics, and automated controls.
Practical Exercises: Hands-on training sessions that allow operators to practice and refine their skills in real-world scenarios. This helps in building confidence and competence.
Regular training ensures that operators remain proficient in their roles and can adapt to new challenges and advancements in excavator technology.
Benefits of a Skilled Operator
The advantages of having well-trained operators extend beyond immediate productivity gains. They include:
Increased Efficiency: Skilled operators can complete tasks more quickly and with greater precision, reducing the overall time needed for projects.
Reduced Wear and Tear: Proper operation techniques minimize unnecessary strain on the excavator, leading to less frequent breakdowns and longer machine lifespan.
Enhanced Safety: Knowledgeable operators are more likely to follow safety protocols, reducing the risk of accidents and injuries on the job site.
Cost Savings: Efficient operation reduces fuel consumption and maintenance costs. Additionally, fewer accidents and breakdowns translate to lower repair expenses and insurance premiums.
Higher Job Satisfaction: Well-trained operators typically feel more confident and competent in their roles, leading to higher job satisfaction and retention rates.
Use the Right Attachments
Using the correct attachments for specific tasks is essential for maximizing the efficiency and productivity of your excavator. Proper attachments make tasks easier, faster, and safer. Here’s a detailed look at the importance of matching attachments to tasks, the benefits of using the correct tools, and the necessity of regular inspection of attachments.
Matching Attachments to Tasks
Each excavation task has unique requirements, and using the right attachment can significantly impact the performance of your machine. Key considerations include:
Bucket Types: Different buckets are designed for various types of digging. For example, a trenching bucket is ideal for narrow, deep trenches, while a grading bucket is best for leveling and finishing.
Hydraulic Hammers: For breaking through concrete or rock, a hydraulic hammer attachment is more effective than a bucket. This specialized tool delivers powerful blows to break up hard materials efficiently.
Augers: When drilling holes for posts or foundations, an auger attachment is essential. It allows for precise and quick drilling, saving time and effort.
Thumbs and Grapples: For handling materials like logs, rocks, or demolition debris, thumbs and grapple attachments provide a secure grip and improve material handling capabilities.
Using the appropriate attachment for each task ensures that the excavator performs optimally, reducing the time and effort required to complete the job.
Benefits of Using the Correct Tools
Increased Productivity: The correct attachment allows for faster and more efficient task completion. For instance, using a rock bucket in rocky terrain can significantly speed up the digging process compared to a standard bucket.
Reduced Wear and Tear: Proper tools minimize unnecessary strain on the excavator. Using a hammer for breaking concrete instead of a bucket prevents damage to the machine and the attachment.
Enhanced Precision: Specialized attachments provide greater accuracy. An auger can drill precise holes, while a grading bucket can create a smooth, even surface.
Safety Improvements: The right attachment can make a task safer. Grapples and thumbs secure heavy or awkward materials, reducing the risk of dropping loads and causing accidents.
Cost Efficiency: Efficient tool use reduces fuel consumption and operational time, leading to cost savings. Additionally, using the right attachment prevents premature wear and reduces maintenance expenses.
Overall, matching the correct attachments to the task at hand enhances the performance and safety of your excavator, leading to better project outcomes and lower operational costs.
Regular Inspection of Attachments
To ensure continued efficiency and safety, attachments must be regularly inspected and maintained. Key practices include:
Visual Inspections: Before and after use, check attachments for visible signs of wear, damage, or deformities. Look for cracks, bent parts, or excessive wear on teeth and edges.
Functional Testing: Periodically test attachments to ensure they are working correctly. For example, check that hydraulic attachments are properly connected and that there are no leaks or pressure drops.
Maintenance Schedule: Follow the manufacturer’s recommended maintenance schedule for each attachment. This includes lubricating moving parts, tightening bolts and connections, and replacing worn components.
Storage: Store attachments properly when not in use. Keeping them in a dry, protected environment prevents rust and deterioration, extending their lifespan.
Efficient Digging Techniques
Implementing efficient digging techniques is crucial for maximizing the performance and productivity of your excavator. By optimizing positioning, minimizing unnecessary movements, and following best practices for faster digging, you can significantly improve your operational efficiency. Here’s how to achieve this.
Proper Positioning and Depth
Correct positioning and maintaining appropriate digging depth are fundamental to efficient excavation:
Optimal Placement: Position the excavator on stable, level ground to ensure stability and prevent tipping. This positioning also allows for better control and reach.
Strategic Location: Place the excavator to cover a large portion of the digging area without frequent repositioning.
Correct Depth: Maintain the right depth for each dig. Over-digging wastes time and fuel, while under-digging requires additional passes. Use depth indicators or GPS systems to ensure accuracy.
Boom and Arm Placement: Position the boom and arm to maximize the bucket’s digging power. Keeping the boom low and the arm extended correctly can increase efficiency.
Proper positioning reduces effort and time, enhancing overall productivity.
Avoiding Unnecessary Movements
Minimizing unnecessary movements conserves energy, reduces wear and tear, and improves digging efficiency:
Plan Your Path: Plan the excavation path to avoid redundant passes and repositioning.
Smooth Operations: Use smooth, controlled movements instead of rapid, jerky actions. This approach is more efficient and reduces stress on the machine.
Bucket Fill Optimization: Aim for full bucket loads with each pass to maximize efficiency.
Reduced Swing Radius: Minimize the swing radius by positioning the excavator so that the digging area is close to the dumping area. This reduces the time and energy spent in swinging the arm.
By avoiding unnecessary movements, you save time and reduce operational costs.
Tips for Faster Digging
Adopting certain techniques can help you dig faster without compromising precision or safety:
Use the Right Bucket: Select a bucket appropriate for the soil type and the task at hand. A bucket with teeth is ideal for rocky soil, while a smooth-edged bucket works better in soft soil.
Proper Trenching Technique: For trenching, start with a shallow cut to establish the trench line, then progressively deepen the trench. This method prevents sidewall collapse and makes digging easier.
Bench Excavation: When digging deep, use bench excavation techniques by creating a series of stepped levels. This method provides better stability and efficiency.
Cycle Time Optimization: Focus on reducing cycle times by synchronizing arm, boom, and bucket movements. Efficient coordination of these movements can speed up the digging process.
Operator Comfort: Ensure the operator’s comfort by adjusting the seat and controls to reduce fatigue. A comfortable operator is more productive and less prone to errors.
Clear Vision: Maintain a clear line of sight to the digging area. Clean windows and proper lighting ensure that the operator can see clearly, reducing the chances of mistakes.
By incorporating these tips into your digging practices, you can achieve faster and more efficient excavation, enhancing overall project productivity.
Technology Integration
Integrating modern technology into excavator operations can significantly enhance efficiency, accuracy, and overall productivity. Leveraging advancements such as GPS, telematics, and automated systems can streamline processes and reduce operational costs. Here’s a detailed look at how technology integration can improve excavator efficiency.
Use of GPS and Telematics
GPS and telematics are powerful tools that provide real-time data and location tracking, essential for optimizing excavator performance:
Precision and Accuracy: GPS technology allows for precise positioning, ensuring that excavation is carried out accurately according to project specifications. This reduces the likelihood of errors and rework.
Real-Time Tracking: Telematics systems track the excavator’s location, movement, and performance in real time. This information helps in monitoring productivity and identifying areas for improvement.
Fleet Management: Telematics enable better management of multiple machines on a job site. Managers can track equipment usage, schedule maintenance, and allocate resources more efficiently.
Operational Insights: Data collected from GPS and telematics systems provide valuable insights into machine utilization, fuel consumption, and idle times. Analyzing this data helps in making informed decisions to enhance efficiency.
Implementing GPS and telematics systems ensures that your excavator operations are precise, well-monitored, and optimized for performance.
Automated Systems and Software
Automation and specialized software solutions further enhance excavator efficiency by simplifying complex tasks and improving consistency:
Automated Controls: Modern excavators can be equipped with automated control systems that assist with tasks such as digging, grading, and trenching. These systems use sensors and GPS data to guide the machine, ensuring accurate and efficient operations.
3D Modeling Software: Software that creates 3D models of the excavation site can be integrated with the excavator’s control system. This allows operators to visualize the project and follow the design with high precision.
Maintenance Scheduling Software: Software that schedules and tracks maintenance activities ensures that the excavator is serviced regularly, preventing unexpected breakdowns and prolonging the machine’s lifespan.
Data Analytics Tools: These tools analyze operational data to identify patterns, inefficiencies, and opportunities for improvement. Predictive analytics can forecast potential issues before they occur, allowing for proactive maintenance.
Adopting automated systems and specialized software streamlines operations, reduces manual errors, and enhances overall efficiency.
Benefits of Modern Technology
The integration of modern technology into excavator operations offers numerous benefits:
Increased Productivity: Automation and precise control systems enable faster and more accurate completion of tasks, boosting overall productivity.
Cost Savings: Efficient use of resources, reduced fuel consumption, and minimized downtime due to predictive maintenance lead to significant cost savings.
Enhanced Safety: Automated systems reduce the risk of operator errors, leading to safer job sites. Real-time monitoring also helps in quickly identifying and addressing safety hazards.
Environmental Impact: Optimized fuel consumption and efficient operations contribute to a lower environmental footprint. Reduced idle times and precise digging reduce unnecessary emissions.
Improved Decision-Making: Access to real-time data and operational insights allows for better decision-making, ensuring that projects are completed on time and within budget.
Operator Assistance: Technology assists operators in performing their tasks more effectively, reducing fatigue and improving overall job satisfaction.
Incorporating modern technology into your excavator operations not only enhances efficiency and productivity but also provides a competitive edge in the industry.
Fuel Management
Efficient fuel management is crucial for optimizing excavator performance, reducing operational costs, and minimizing environmental impact. Implementing best practices for fuel usage, conducting regular fuel checks, and investing in fuel-efficient models can significantly enhance your excavator’s efficiency. Here’s how to manage fuel effectively.
Efficient Fuel Usage Practices
Adopting efficient fuel usage practices can lead to substantial savings and improved machine performance:
Optimal Engine Load: Avoid running the excavator at maximum power continuously. Operate at an optimal engine load to balance performance and fuel consumption.
Minimize Idling: Excessive idling wastes fuel and increases engine wear. Turn off the engine during extended periods of inactivity to save fuel.
Proper Throttle Use: Use the throttle appropriately based on the task. For light-duty operations, lower throttle settings are sufficient and help in conserving fuel.
Scheduled Work Cycles: Plan and organize work cycles to minimize unnecessary movements and idle times. Efficient task sequencing reduces fuel consumption.
Efficient Travel Routes: Plan the shortest and most efficient routes for the excavator to travel on the job site, reducing fuel used for unnecessary movements.
Implementing these practices ensures that fuel is used efficiently, reducing costs and extending the operational life of the excavator.
Regular Fuel Checks
Regular monitoring and maintenance of the fuel system are essential for maintaining fuel efficiency:
Fuel Quality: Use high-quality fuel to prevent contaminants from entering the fuel system. Contaminated fuel can cause engine inefficiency and damage.
Fuel Filters: Check and replace fuel filters regularly to ensure clean fuel reaches the engine. Clogged filters restrict fuel flow and reduce efficiency.
Leak Inspections: Regularly inspect the fuel system for leaks. Fuel leaks not only waste fuel but also pose safety and environmental hazards.
Fuel Consumption Monitoring: Keep track of fuel consumption patterns. Sudden increases in fuel use may indicate underlying issues such as leaks, inefficient operation, or engine problems.
Regular Servicing: Ensure that the excavator is serviced regularly as per the manufacturer’s guidelines. Regular servicing keeps the fuel system in good condition and maintains optimal performance.
Regular fuel checks and maintenance help in identifying issues early and maintaining the efficiency and reliability of the excavator.
Benefits of Fuel-Efficient Models
Investing in fuel-efficient excavator models offers long-term advantages that enhance overall operational efficiency:
Lower Operating Costs: Fuel-efficient models consume less fuel for the same amount of work, significantly reducing operating costs over time.
Reduced Environmental Impact: Lower fuel consumption results in fewer emissions, making fuel-efficient models more environmentally friendly.
Advanced Technology: Fuel-efficient excavators often come equipped with advanced technologies such as improved engine designs, better hydraulic systems, and intelligent control systems that optimize fuel use.
Longer Engine Life: Efficient fuel usage reduces the strain on the engine, leading to longer engine life and fewer maintenance issues.
Higher Resale Value: Fuel-efficient models tend to have a higher resale value due to their cost-saving benefits and lower environmental impact.
By choosing fuel-efficient models, you not only save on fuel costs but also contribute to sustainability and gain other operational benefits.
Proper Tire and Track Maintenance
Maintaining the tires and tracks of your excavator is crucial for ensuring optimal performance, safety, and efficiency. Regular checks for wear and tear, proper alignment, and ensuring good traction are key components of effective maintenance. Here’s a detailed look at each aspect.
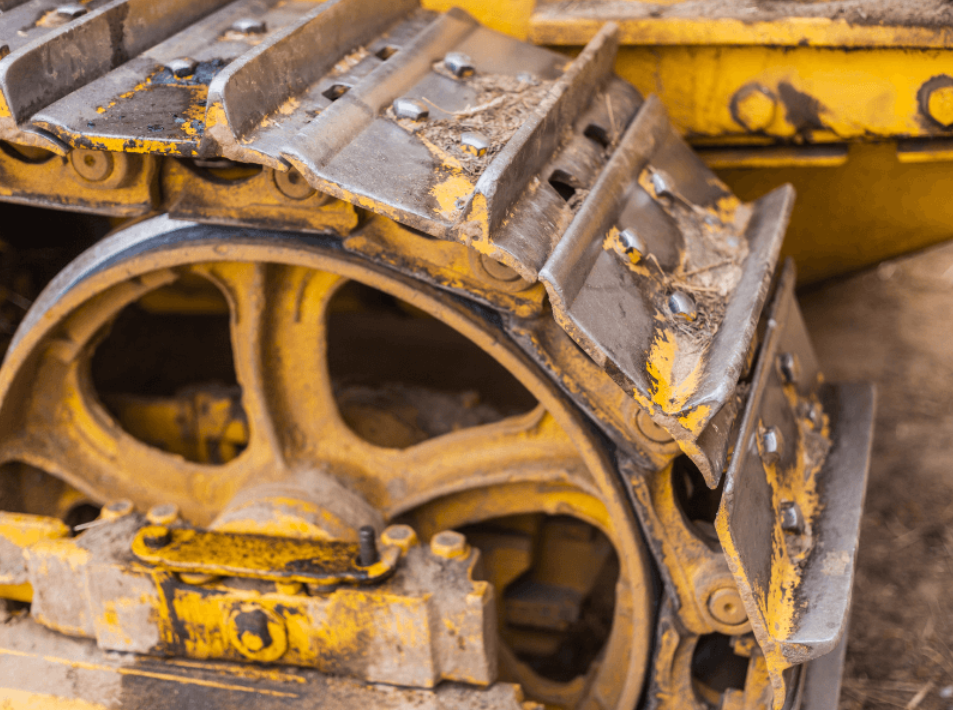
Checking for Wear and Tear
Regular inspection of tires and tracks for wear and tear is essential to prevent unexpected breakdowns and extend their lifespan:
Visual Inspections: Conduct daily visual inspections of tires and tracks. Look for visible signs of damage such as cuts, cracks, punctures, and worn-out treads.
Depth Measurements: Measure the tread depth of tires regularly. Tires with insufficient tread depth can lose traction and become unsafe.
Track Tension: Check the tension of the tracks. Tracks that are too tight or too loose can cause premature wear and tear. Follow the manufacturer’s guidelines for proper tension levels.
Component Wear: Inspect other components like sprockets, rollers, and idlers for wear and damage. Worn components can lead to uneven wear and reduce the efficiency of the tracks.
Regularly checking for wear and tear ensures that your excavator operates safely and efficiently, preventing costly downtime due to unexpected failures.
Proper Alignment
Proper alignment of tires and tracks is crucial for maintaining the stability and efficiency of the excavator:
Track Alignment: Misaligned tracks can cause uneven wear and tear, reducing their lifespan. Ensure tracks are properly aligned by regularly checking their position and making adjustments as needed.
Tire Alignment: For wheeled excavators, proper tire alignment is essential to prevent uneven wear. Misaligned tires can lead to poor handling and increased fuel consumption.
Steering and Suspension: Regularly inspect the steering and suspension systems. Properly functioning steering and suspension help maintain alignment and improve overall machine stability.
Make alignment adjustments part of your regular maintenance routine. Frequent checks and timely adjustments can prevent minor misalignments from becoming major issues.
Ensuring proper alignment reduces wear and tear, improves fuel efficiency, and enhances the overall performance of your excavator.
Importance of Good Traction
Good traction is vital for the efficient and safe operation of an excavator, particularly in challenging terrains:
Safety: Adequate traction prevents slippage, especially when operating on slopes, loose soil, or wet conditions. This enhances the safety of the operator and the stability of the excavator.
Efficiency: Good traction allows for better transfer of power from the machine to the ground, improving digging and loading efficiency. It ensures that the excavator can move smoothly and operate effectively.
Reduced Wear: Tires and tracks with good traction experience less slippage and excessive wear. This not only extends their lifespan but also reduces the frequency of maintenance and replacements.
Fuel Efficiency: Proper traction reduces the amount of power needed to move the excavator, leading to better fuel efficiency. Less slippage means less wasted energy, lowering operational costs.
Ensuring good traction through regular maintenance of tires and tracks is essential for the safe, efficient, and cost-effective operation of your excavator.
Job Site Management
Efficient job site management is key to maximizing the productivity and efficiency of excavator operations. By organizing the site effectively, reducing idle time, and ensuring a well-planned layout, you can enhance operational efficiency and minimize costs. Here’s how to manage your job site for optimal performance.
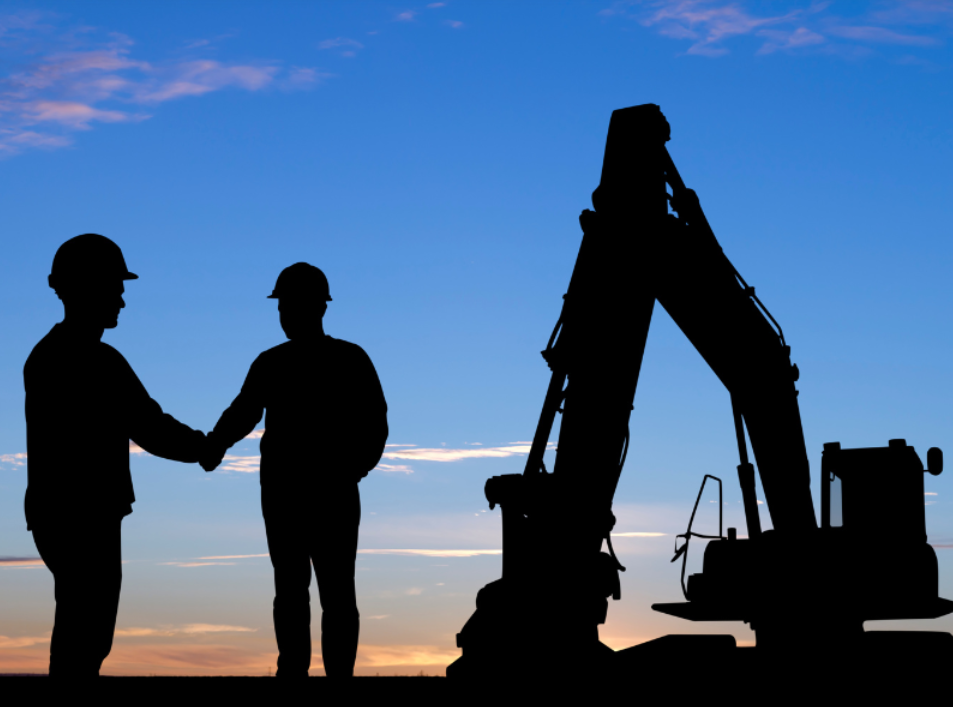
Organizing the Site Efficiently
A well-organized job site is essential for smooth and efficient operations. Key strategies include:
Clear Pathways: Establish clear and safe pathways for the movement of equipment and materials. This reduces the chances of accidents and ensures that operations run smoothly.
Designated Zones: Allocate specific areas for different activities such as material storage, equipment parking, and waste disposal. Keeping these zones organized prevents clutter and confusion.
Efficient Material Handling: Position materials and supplies close to the areas where they will be used. This minimizes the time and effort required to transport materials across the site.
Communication Systems: Implement robust communication systems to ensure all team members are aware of the site layout and any changes. Effective communication enhances coordination and prevents misunderstandings.
Safety Measures: Ensure that safety measures are in place and clearly marked. This includes proper signage, barriers around hazardous areas, and clear demarcation of walkways and operational zones.
Organizing the job site efficiently reduces delays, enhances safety, and improves overall productivity.
Reducing Idle Time
Minimizing idle time is crucial for improving the efficiency and cost-effectiveness of excavator operations. Strategies to achieve this include:
Task Scheduling: Plan tasks meticulously to ensure that each phase of the project flows seamlessly into the next. Avoid gaps between tasks that can lead to equipment and personnel standing idle.
Equipment Readiness: Ensure that all equipment is ready and in good working condition before starting the job. This includes performing pre-operation checks and routine maintenance.
Operator Coordination: Coordinate the activities of operators and other personnel to prevent waiting times. For instance, ensure that dump trucks are ready and waiting when the excavator is loading materials.
Fuel Management: Implement efficient fuel management practices to avoid downtime due to refueling. This includes refueling during scheduled breaks rather than in the middle of active operations.
Real-Time Monitoring: Use telematics and other monitoring systems to track equipment usage and idle times. Analyzing this data helps identify and address inefficiencies promptly.
By actively managing and reducing idle time, you can keep your excavator and crew working efficiently, leading to faster project completion and lower costs.
Importance of a Well-Planned Layout
A well-planned job site layout is fundamental to efficient excavator operations. The benefits of a thoughtful layout include:
Optimized Workflow: A strategic layout facilitates a smooth workflow, where each step of the operation is logically connected to the next. This reduces unnecessary movements and improves overall efficiency.
Reduced Travel Distance: Position the excavator, materials, and dumping areas in close proximity to minimize travel distances. This reduces fuel consumption and wear on the machine.
Safety Enhancement: A well-organized layout reduces the risk of accidents by clearly defining operational zones, pathways, and safety barriers. This ensures that equipment and personnel can move safely around the site.
Effective Resource Allocation: Proper layout planning allows for better allocation of resources, including manpower and machinery. This ensures that all resources are utilized efficiently without overlap or underuse.
Flexibility and Adaptability: A well-planned layout is also adaptable, allowing for quick adjustments as project requirements change. This flexibility helps in maintaining efficiency even when unexpected changes occur.
The importance of a well-planned layout cannot be overstated. It is the foundation of efficient operations, ensuring that all activities are coordinated and executed smoothly.
Conclusion
These simple tips can help you get the most out of your excavator, boosting your work output and minimizing machine breakdowns. HOLIGHT Industrial Group offers a complete selection of second-hand excavators, parts, and expert technical assistance. Our experienced team is here to answer your questions and recommend the best operating practices for your digging jobs. Get in touch with us today to learn more!