Road rollers, also known as roller-compactors, are crucial machines in the construction industry. They play a vital role in the process of road building and other large-scale construction projects by compacting soil, gravel, concrete, and asphalt. This compaction process is essential for creating a solid and stable foundation, ensuring the durability and longevity of roads and other structures. The effectiveness of a road roller can directly influence the quality of the project, making it an indispensable piece of equipment on any construction site. This comprehensive guide aims to provide a detailed overview of operating a road roller, ensuring that both novice and experienced operators can maximize efficiency and safety.
1.Components of a Road Roller
Understanding the various components of a road roller is essential for efficient operation and maintenance. Each part plays a critical role in the overall functionality of the machine. Here’s a detailed look at the key components:
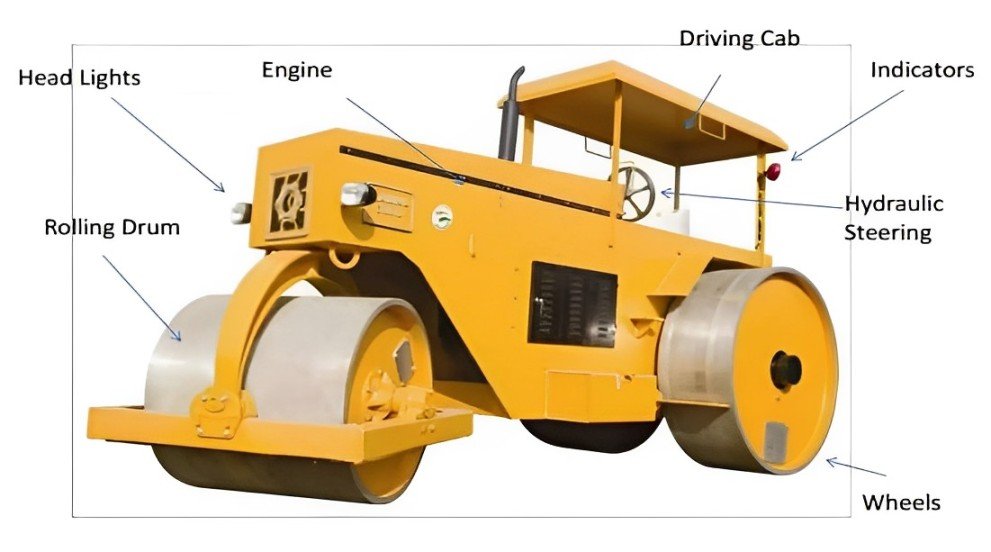
Drum
The drum is the most recognizable part of a road roller. It is the large, cylindrical component at the front (or sometimes the back) of the roller, and its primary function is to compact the material being worked on. There are different types of drums depending on the specific application:
Smooth Drum: Ideal for compacting granular materials like gravel, sand, and asphalt. Smooth drums provide a flat, even surface and are commonly used in finishing operations.
Padded or Sheepsfoot Drum: Designed for compacting cohesive materials such as clay or silt. These drums have protruding pads that penetrate the material, providing deeper compaction.
Vibratory Drum: Equipped with an internal mechanism that causes the drum to vibrate, enhancing compaction efficiency. This type is particularly useful for asphalt and granular materials.
Engine
The engine is the powerhouse of the road roller. It provides the necessary energy to move the machine and power its various functions. Key aspects of the engine include:
Diesel or Gasoline Engine: Most road rollers are equipped with either a diesel or gasoline engine, each with its own advantages. Diesel engines are known for their fuel efficiency and durability, while gasoline engines are typically easier to start and maintain.
Horsepower: The power output of the engine, measured in horsepower (HP), determines the roller’s capability to handle different types of work. Higher horsepower engines are required for heavy-duty tasks.
Cooling System: To prevent overheating, the engine is equipped with a cooling system that usually includes a radiator and fan. Regular maintenance of the cooling system is crucial to ensure the engine operates smoothly.
Cab and Controls
The cab is where the operator sits and controls the road roller. It is designed for comfort and ease of use, with various controls and instruments to manage the machine’s functions. Key features include:
Operator Seat: Adjustable seats with suspension systems provide comfort, reducing operator fatigue during long hours of operation.
Steering Wheel or Joystick: Used to maneuver the road roller. Some modern rollers are equipped with joysticks for more precise control.
Control Panel: Contains various gauges and switches, including the ignition switch, throttle control, brake levers, and instrument panel displaying engine speed, fuel level, and other critical data.
Visibility: The cab is designed to provide maximum visibility of the work area, ensuring the operator can see obstacles and avoid accidents.
Water System (if applicable)
Some road rollers, particularly those used for asphalt compaction, are equipped with a water system. This system helps to prevent the asphalt from sticking to the drum, ensuring a smooth finish. Components of the water system include:
Water Tank: Stores water used for spraying onto the drum. The size of the tank varies depending on the roller model and intended usage.
Spray Bars and Nozzles: Positioned near the drum, these components distribute water evenly across the drum’s surface. Proper functioning of the spray system is crucial for effective operation.
Water Pump: Pumps water from the tank to the spray bars. Regular maintenance of the water pump is necessary to ensure consistent water flow.
Understanding these components is essential for anyone operating a road roller. Each part must be in good working condition to ensure the machine operates efficiently and safely. Regular inspections and maintenance of these components will help extend the life of the road roller and maintain its performance on the job site.
2.Preparation Before Operation
Proper preparation before operating a road roller is crucial to ensure both safety and efficiency. This includes performing safety checks, inspecting the roller, and verifying fluid levels and tire pressure. Here’s a detailed guide on how to prepare a road roller before operation.
Safety Checks
Safety should always be the first priority on any construction site. Before starting the road roller, perform these essential safety checks:
Personal Protective Equipment (PPE): Ensure that all operators and nearby workers are wearing the appropriate PPE. This includes hard hats, safety glasses, high-visibility vests, gloves, and steel-toed boots. PPE is critical to protect against potential hazards on the construction site.
Clear the Area: Inspect the work area to ensure it is free from obstacles, debris, and unauthorized personnel. Establish a safe perimeter around the operating zone to prevent accidents.
Emergency Plan: Make sure there is an emergency plan in place. All operators should know the locations of emergency exits, first aid kits, fire extinguishers, and communication devices. In case of an emergency, everyone should be aware of the proper procedures.
Operator Training: Verify that the operator is properly trained and certified to operate the road roller. Inexperienced operators should not use the machine without proper supervision. Training ensures that operators are familiar with the machine’s controls and safety procedures.
Inspection of the Roller
Conducting a thorough inspection of the road roller before operation is vital to identify any potential issues that could affect performance or safety. Here are the key steps:
Visual Inspection: Walk around the machine and visually inspect it for any obvious signs of damage or wear. Look for leaks, loose bolts, and damaged parts. Address any issues before operating the roller.
Drum and Tires: Examine the drum for cracks, dents, or excessive wear. For rollers with tires, check the tires for cuts, punctures, or uneven wear patterns. Proper drum and tire conditions are essential for effective compaction.
Hydraulic Hoses: Inspect hydraulic hoses for signs of wear, leaks, or cracks. Damaged hoses can lead to hydraulic fluid leaks, which can be hazardous. Ensure that all hoses are in good condition.
Lights and Signals: Ensure that all lights, signals, and reflectors are functioning correctly. This is particularly important for visibility in low-light conditions. Proper lighting ensures that the roller can be seen by other workers and vehicles on the site.
Operator Controls: Test all operator controls, including the steering, brakes, and throttle. Make sure they are functioning smoothly and respond accurately. Functional controls are essential for safe and effective operation.
Safety Features: Check that all safety features, such as seat belts, backup alarms, and emergency shutoff switches, are in working order. These features are designed to protect the operator and others on the site.
Checking Fluid Levels and Tire Pressure
Maintaining proper fluid levels and tire pressure is essential for the smooth operation of a road roller. Here’s what to check:
Engine Oil: Check the engine oil level using the dipstick. Ensure that the oil level is within the recommended range. If necessary, top up the oil with the correct grade specified by the manufacturer. Proper engine oil levels are crucial for engine performance and longevity.
Hydraulic Fluid: Inspect the hydraulic fluid reservoir and ensure the fluid level is adequate. Low hydraulic fluid can impair the machine’s performance and cause damage to the hydraulic system. Maintain the fluid at the recommended level.
Coolant: Check the coolant level in the radiator and overflow tank. Adequate coolant is necessary to prevent the engine from overheating. Top up the coolant if needed, using the appropriate type recommended by the manufacturer.
Fuel: Ensure that the fuel tank is full. Running out of fuel during operation can cause unnecessary delays and potential damage to the engine. Use the correct type of fuel specified by the manufacturer.
Transmission Fluid: Verify that the transmission fluid level is correct. This is crucial for the smooth operation of the machine’s transmission system. Check the manufacturer’s guidelines for the proper fluid type and level.
Tire Pressure: For road rollers with tires, check the tire pressure using a tire gauge. Inflate the tires to the manufacturer’s recommended pressure. Proper tire pressure ensures optimal performance and reduces the risk of tire damage.
By thoroughly preparing the road roller before operation, you can significantly reduce the risk of accidents and equipment failure. These preparation steps ensure that the machine operates efficiently, contributing to the overall success of the construction project. Regularly performing these checks and inspections will also help extend the lifespan of the road roller, ensuring it remains a valuable asset on the job site.
3.Operating the Road Roller
Operating a road roller effectively and safely requires understanding how to start the machine, familiarity with the controls and instruments, and mastering basic maneuvers such as moving forward, reversing, and turning. Here’s a detailed guide to help you operate a road roller.
Starting the Roller
Starting a road roller involves several steps to ensure the machine is ready for operation:
Pre-Start Checks: Before starting the roller, ensure all safety checks, inspections, and fluid level verifications have been completed. Make sure the area around the roller is clear of obstacles and personnel.
Enter the Cab: Climb into the cab using the provided steps and handholds. Ensure that the operator’s seat is adjusted for comfort and visibility.
Fasten Seat Belt: Fasten the seat belt to ensure your safety while operating the machine.
Ignition: Insert the key into the ignition switch and turn it to the “On” position. Allow the warning lights and gauges to complete their self-check cycles.
Start the Engine: Turn the key to the “Start” position to start the engine. Release the key once the engine starts. If the engine does not start immediately, wait a few seconds before trying again to avoid flooding the engine.
Warm Up: Allow the engine to warm up for a few minutes. This helps the engine reach optimal operating temperature and ensures that all systems are functioning correctly.
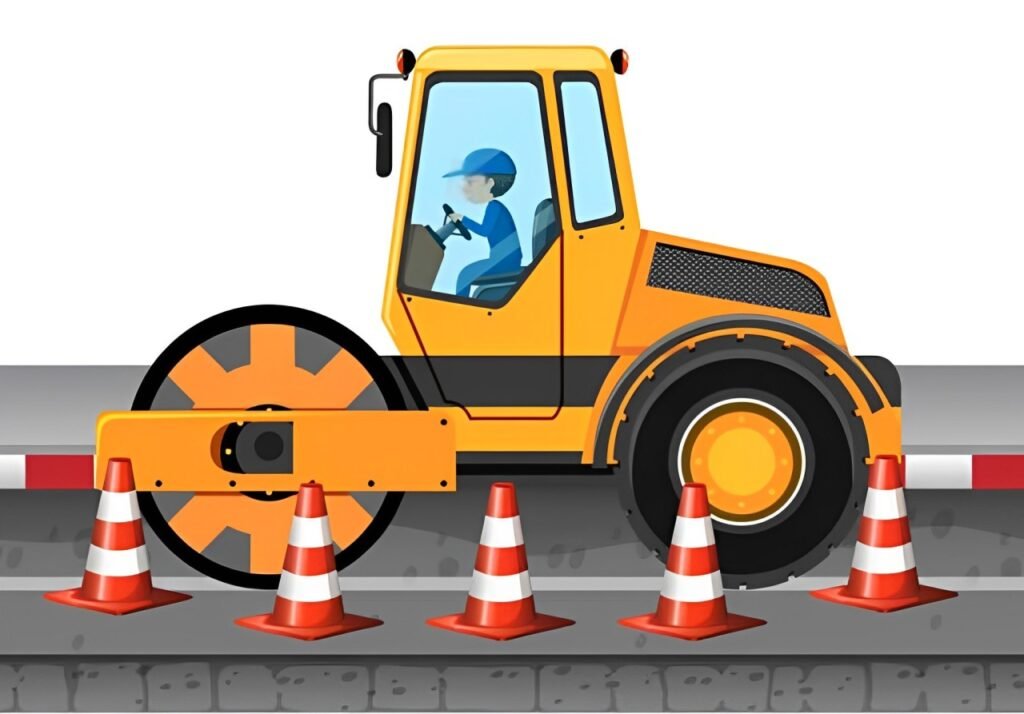
Understanding Controls and Instruments
Familiarity with the controls and instruments is crucial for safe and efficient operation. Here are the key controls and instruments typically found in a road roller cab:
Steering Wheel or Joystick: Used to control the direction of the roller. Steering wheels are common in older models, while modern rollers may use joysticks for more precise control.
Throttle Control: Regulates the engine speed. Increasing the throttle provides more power for heavy-duty tasks, while reducing it conserves fuel during lighter work.
Brake Pedals: Used to slow down or stop the roller. There are typically separate pedals for the service brake and the parking brake. Make sure to understand the function of each brake.
Gear Selector: Controls the transmission, allowing you to select different gears for forward and reverse movements. Familiarize yourself with the gear positions before operating the roller.
Instrument Panel: Displays critical information about the machine, including engine speed (RPM), fuel level, hydraulic pressure, and warning lights. Regularly monitor the instrument panel to ensure the roller is operating within safe parameters.
Vibration Control (if applicable): Some road rollers have a control to activate and adjust the vibration function of the drum. Vibration enhances compaction efficiency, especially on granular materials.
Lights and Signals: Controls for headlights, turn signals, and other lights. Ensure they are functioning correctly for safe operation in low-light conditions.
Basic Maneuvers
Mastering basic maneuvers such as moving forward, reversing, and turning is essential for effective operation:
Moving Forward:
Select Gear: Move the gear selector to the forward position.
Release Brake: Gently release the parking brake and service brake.
Throttle: Gradually increase the throttle to start moving forward. Use smooth and controlled movements to maintain stability.
Reversing:
Select Gear: Move the gear selector to the reverse position.
Check Surroundings: Ensure the area behind the roller is clear of obstacles and personnel.
Release Brake: Gently release the parking brake and service brake.
Throttle: Gradually increase the throttle to start moving backward. Use the mirrors and rearview camera (if available) to monitor the area behind you.
Turning:
Steering: Use the steering wheel or joystick to change direction. For tight turns, reduce speed to maintain control.
Monitor Drum Position: Be aware of the position of the drum, especially when turning near obstacles or edges.
Adjust Speed: Slow down before initiating a turn to ensure stability and control.
4.Safety Tips
Safety is paramount when operating a road roller. Proper safety measures help prevent accidents and ensure a safe working environment for operators and other workers on the construction site. Here are essential safety tips, including the use of personal protective equipment (PPE), worksite safety precautions, and handling emergencies.
Personal Protective Equipment (PPE)
Wearing the appropriate PPE is crucial for protecting yourself from potential hazards. Here’s a list of essential PPE for operating a road roller:
Hard Hat: Protects your head from falling objects and bumps.
Safety Glasses or Goggles: Shields your eyes from dust, debris, and other potential hazards.
High-Visibility Vest: Makes you more visible to other workers and machinery operators, especially in low-light conditions.
Gloves: Protect your hands from cuts, abrasions, and chemical exposure.
Steel-Toed Boots: Provides protection for your feet from heavy objects and offers better grip on various surfaces.
Hearing Protection: Use earplugs or earmuffs if you are working in a noisy environment.
Worksite Safety Precautions
Implementing worksite safety precautions ensures a safer environment for everyone on the construction site. Here are key precautions to follow:
Clear Communication: Maintain clear communication with all workers on the site. Use hand signals, two-way radios, or other communication devices to stay in touch.
Establish a Safe Perimeter: Set up barriers and warning signs to mark the operating zone of the road roller. Ensure that unauthorized personnel stay clear of this area.
Inspect the Work Area: Before starting operations, inspect the work area for any obstacles, debris, or hazardous conditions. Remove or mark any potential hazards.
Slow and Steady Movements: Operate the road roller at a controlled speed, especially in congested areas or near the edges of the work zone. Sudden movements can cause accidents or loss of control.
Stay Alert: Always remain vigilant and aware of your surroundings. Watch for other machinery, workers, and obstacles in your path.
Proper Lighting: Ensure that the work area is well-lit, especially during early morning, late evening, or night operations. Proper lighting helps in identifying hazards and maintaining visibility.
Handling Emergencies
Knowing how to handle emergencies can prevent minor issues from escalating into major accidents. Here are steps to handle common emergencies, such as brake failure:
Brake Failure:
Stay Calm: Do not panic. Keep a clear head to handle the situation effectively.
Activate Emergency Brake: If the primary brake fails, use the emergency brake immediately.
Steer to Safety: Steer the road roller towards a safe area, away from workers and obstacles. Use the steering to gradually slow down the machine if the brakes are not functioning.
Stop the Engine: Turn off the engine to bring the machine to a halt if the emergency brake does not work.
Signal for Help: Use a horn, radio, or other communication devices to alert others to the situation. Request assistance from nearby workers or supervisors.
Fire:
Shut Down the Machine: Turn off the engine to stop the fuel supply and reduce the risk of the fire spreading.
Use Fire Extinguisher: If the fire is small and manageable, use a fire extinguisher to put it out. Ensure you know the location and proper use of fire extinguishers on the site.
Evacuate: If the fire is large or uncontrollable, evacuate the area immediately and alert emergency services.
Hydraulic or Fuel Leak:
Stop the Machine: Turn off the engine to prevent further leakage.
Contain the Leak: Use absorbent materials to contain the spill and prevent it from spreading.
Report the Incident: Inform your supervisor and follow the site’s protocol for handling hazardous materials.
Medical Emergency:
Provide First Aid: Administer first aid if you are trained and it is safe to do so.
Call for Help: Contact emergency services and inform your supervisor about the incident.
Assist Until Help Arrives: Stay with the injured person and provide comfort and assistance until professional help arrives.
By following these safety tips, you can ensure a safer work environment and reduce the risk of accidents and injuries while operating a road roller. Always prioritize safety and stay prepared to handle emergencies effectively.
5.Maintenance and Care
Proper maintenance and care of a road roller are essential to ensure its longevity, performance, and safety. A well-maintained machine not only operates more efficiently but also reduces the risk of unexpected breakdowns and costly repairs. This section covers a daily maintenance routine, a regular servicing schedule, and tips for storage and winterization.
Daily Maintenance Routine
Performing daily maintenance checks helps keep the road roller in optimal condition. Here’s a routine to follow each day before operating the machine:
Visual Inspection: Conduct a thorough walk-around inspection. Check for any visible signs of damage, leaks, or wear and tear. Pay special attention to the drum, tires, hydraulic hoses, and lights.
Fluid Levels: Check the levels of engine oil, hydraulic fluid, coolant, and fuel. Ensure they are within the recommended ranges. Top up any fluids that are low using the appropriate types specified by the manufacturer.
Air Filters: Inspect the air filters for dirt and debris. Clean or replace them if necessary to ensure the engine receives clean air.
Drum and Tires: Examine the drum for cracks or excessive wear. For rollers with tires, check the tire pressure and look for any cuts or punctures. Inflate tires to the recommended pressure if needed.
Controls and Instruments: Test all controls, including the steering, brakes, throttle, and vibration control. Ensure that all instruments and gauges on the control panel are functioning correctly.
Grease Points: Lubricate all grease points as per the manufacturer’s guidelines. Proper lubrication reduces wear and tear on moving parts.
Battery: Check the battery terminals for corrosion and ensure the battery is securely mounted. Clean the terminals and tighten connections if necessary.
Safety Features: Verify that all safety features, such as seat belts, backup alarms, and emergency shutoff switches, are operational.
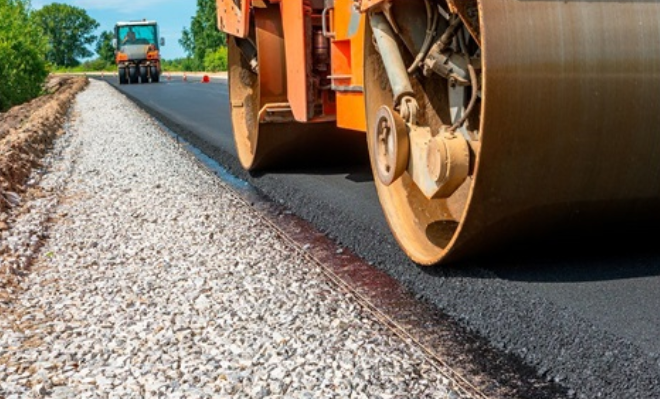
Regular Servicing Schedule
In addition to daily maintenance, adhere to a regular servicing schedule based on the manufacturer’s recommendations. Regular servicing involves more comprehensive checks and maintenance tasks to ensure the long-term reliability of the road roller. Here’s a typical servicing schedule:
Weekly Checks:
Inspect the machine’s overall condition more thoroughly.
Clean the machine, removing dirt and debris from critical areas.
Check for loose bolts and tighten them as needed.
Monthly Maintenance:
Change the engine oil and replace the oil filter.
Inspect the hydraulic system, including hoses, fittings, and fluid levels. Replace any damaged hoses.
Check the coolant system, including the radiator and hoses, for leaks or blockages.
Inspect the fuel system, including the fuel filter and lines, for leaks or clogs.
Perform a detailed inspection of the drum and tires, addressing any wear or damage.
Quarterly or Semi-Annual Servicing:
Perform a comprehensive inspection of the entire machine.
Change the hydraulic fluid and replace the hydraulic filter.
Inspect and service the transmission system.
Check and adjust the engine valves, if applicable.
Test the electrical system, including wiring and connections.
Perform a thorough inspection and maintenance of the drum’s vibratory system (if equipped).
Annual Servicing:
Conduct a complete overhaul of the machine, including all the checks mentioned above.
Replace any worn or damaged parts.
Perform a detailed inspection of the engine, transmission, hydraulic system, and electrical components.
Update any software or control system firmware, if applicable.
Storage Tips and Winterization
Proper storage and winterization of the road roller are crucial, especially if the machine will be idle for an extended period or exposed to harsh weather conditions. Here are some tips for storage and winterization:
Clean the Machine: Thoroughly clean the road roller, removing all dirt, debris, and asphalt residue. Pay special attention to the drum, undercarriage, and cooling system.
Fluid Levels: Check and top up all fluid levels. Consider adding a fuel stabilizer to the fuel tank to prevent fuel degradation during storage.
Lubrication: Apply a generous amount of grease to all lubrication points. This helps protect moving parts from rust and corrosion.
Battery Maintenance: Disconnect the battery or use a trickle charger to maintain its charge. Store the battery in a cool, dry place if it is removed from the machine.
Protect from Elements: Store the road roller in a sheltered area, such as a garage or storage shed, to protect it from the elements. If indoor storage is not available, use a high-quality cover to shield the machine from rain, snow, and sunlight.
Tires: If the roller has tires, ensure they are properly inflated before storage. Consider using tire covers to protect them from UV damage.
Engine and Exhaust: Cover the engine and exhaust openings to prevent moisture and pests from entering.
Winterization: For areas with freezing temperatures, ensure the coolant system is filled with antifreeze. Drain any water from the machine’s systems to prevent freezing and potential damage.
By following these maintenance and care guidelines, you can ensure that your road roller remains in excellent working condition, providing reliable performance and longevity. Regular maintenance and proper storage practices are key to maximizing the value and efficiency of your road roller.
6.Common Issues and Troubleshooting
Even with regular maintenance, road rollers can encounter issues that affect their performance. Understanding how to identify and troubleshoot common problems such as overheating, hydraulic system issues, and electrical problems can help minimize downtime and keep your machine running smoothly. Here’s a guide to troubleshooting these common issues.
Overheating
Overheating is a common problem in road rollers, especially during heavy use or in hot weather conditions. Overheating can lead to serious engine damage if not addressed promptly. Here’s how to troubleshoot and resolve overheating issues:
Check Coolant Levels: Low coolant levels are a primary cause of overheating. Check the coolant reservoir and radiator to ensure they are filled to the appropriate levels. Top up the coolant if necessary, using the type specified by the manufacturer.
Inspect the Radiator: Ensure the radiator is clean and free of obstructions. Dirt, debris, and asphalt can block the radiator fins, reducing cooling efficiency. Clean the radiator with compressed air or water, being careful not to damage the fins.
Check for Leaks: Inspect the coolant system for leaks in hoses, the radiator, and the water pump. Replace any damaged or leaking components.
Fan Operation: Verify that the engine cooling fan is operating correctly. A malfunctioning fan can significantly reduce cooling performance. Check the fan belt for wear and proper tension, and ensure the fan blades are not damaged.
Thermostat: A stuck or malfunctioning thermostat can prevent coolant from flowing through the engine, causing overheating. Replace the thermostat if it is not functioning correctly.
Water Pump: Ensure the water pump is working correctly to circulate coolant through the engine. A failing water pump can cause insufficient coolant flow, leading to overheating.
Hydraulic System Problems
Hydraulic systems are crucial for the operation of a road roller, controlling functions such as steering, braking, and drum vibration. Here’s how to troubleshoot common hydraulic system issues:
Check Hydraulic Fluid Levels: Low hydraulic fluid levels can cause system malfunctions. Check the hydraulic fluid reservoir and top up as necessary with the correct type of fluid.
Inspect for Leaks: Hydraulic fluid leaks are a common issue. Inspect all hoses, fittings, and seals for signs of leakage. Replace any damaged or worn components to prevent further leaks.
Filter Condition: A clogged hydraulic filter can restrict fluid flow and reduce system performance. Check and replace the hydraulic filter regularly as per the manufacturer’s recommendations.
Hydraulic Pump: Ensure the hydraulic pump is functioning correctly. Listen for unusual noises such as whining or grinding, which can indicate pump failure. Replace the pump if it is not operating correctly.
Cylinder and Valve Issues: Hydraulic cylinders and valves can wear out or become damaged over time. Inspect these components for signs of wear or damage and replace them if necessary.
Air in the System: Air trapped in the hydraulic system can cause erratic operation and reduced efficiency. Bleed the system to remove any air pockets.
Electrical Issues
Electrical problems can affect various functions of the road roller, including starting, lighting, and control systems. Here’s how to troubleshoot common electrical issues:
Battery Check: A dead or weak battery is a common cause of electrical problems. Check the battery voltage and ensure it is fully charged. Clean the battery terminals and ensure they are securely connected.
Fuses and Relays: Check the fuses and relays for any blown fuses or faulty relays. Replace any that are damaged to restore electrical function.
Wiring and Connections: Inspect the wiring harness and electrical connections for signs of wear, corrosion, or damage. Repair or replace any damaged wiring or connectors to ensure a secure electrical connection.
Starter Motor: If the engine is not starting, the starter motor may be faulty. Listen for clicking sounds when attempting to start the engine, which can indicate a starter motor issue. Replace the starter motor if necessary.
Alternator: Ensure the alternator is charging the battery correctly. Use a multimeter to check the alternator’s output voltage. Replace the alternator if it is not charging the battery adequately.
Control Panel and Instruments: If the control panel or instruments are not functioning, check the connections and wiring behind the panel. Ensure all connectors are securely attached and inspect for any damaged wires.
By understanding these common issues and their solutions, you can effectively troubleshoot and resolve problems with your road roller. Regular maintenance and prompt attention to any signs of trouble will help keep your machine running smoothly and efficiently, minimizing downtime and extending its lifespan.
7.Conclusion
Operating a road roller, like any construction equipment, demands significant attention. Regardless of how straightforward it seems, your safety and the safety of those around you depend on it.
HOLIGHT Industrial Group provides a variety of different road rollers, welcome to contact us for more information about our road rollers.