In the mining industry, efficiency and productivity hinge significantly on the type of heavy equipment utilized. The right machinery not only ensures that operations run smoothly but also contributes to the overall safety and cost-effectiveness of mining projects. Choosing the right equipment involves evaluating various factors, including the type of mining operation, the terrain, the specific tasks to be performed, and the budget. Each piece of equipment serves a distinct purpose, from drilling and blasting to loading and hauling. Therefore, understanding the capabilities and limitations of Different types of machinery are essential for optimizing mining operations.
Types of Heavy Equipment Used in Mining
Excavators
Excavators are essential in mining operations due to their versatility and efficiency in handling various tasks. These machines are primarily used for digging, but their functions extend to grading, site preparation, and material handling. Excavators come in different sizes and configurations, making them suitable for both surface and underground mining.
In surface mining, large excavators are used to remove overburden, the layer of soil and rock overlaying a mineral deposit. Their powerful hydraulic systems allow them to dig through hard materials with ease. Excavators equipped with specialized attachments, such as rock breakers and grapples, can perform additional tasks like breaking apart large rocks and handling debris.
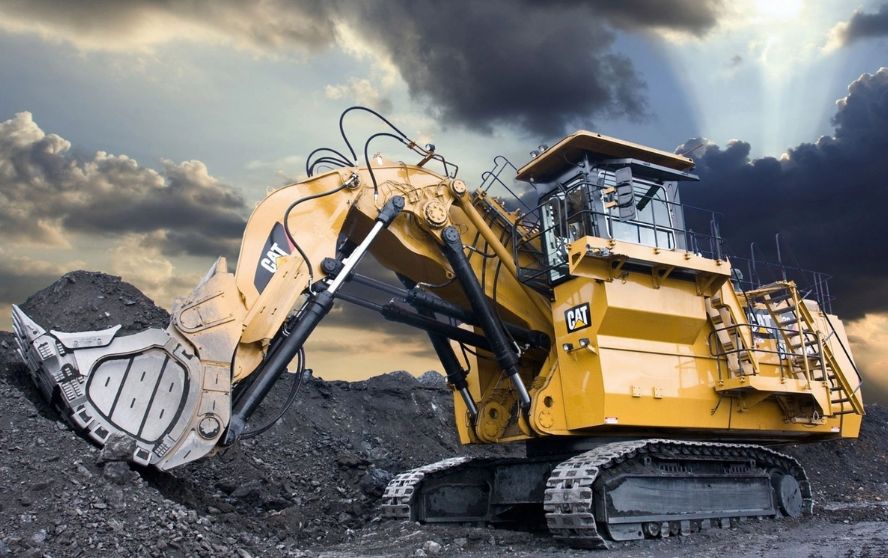
For underground mining, smaller and more maneuverable excavators are used to navigate confined spaces. These machines are often equipped with advanced technology, such as remote control systems, to enhance safety and precision in hazardous environments. Excavators play a crucial role in maintaining productivity and efficiency in mining operations by ensuring that materials are moved quickly and safely.
Bulldozers
Bulldozers are another critical piece of heavy equipment in mining, known for their powerful pushing capabilities. These machines are equipped with a large, flat blade at the front, which is used to push large quantities of soil, rock, and other materials. Bulldozers are indispensable in both surface and underground mining for tasks such as clearing overburden, leveling terrain, and constructing access roads.
In surface mining, bulldozers are often used to clear and level large areas, making it easier for other equipment to operate. They are also employed to create benches and ramps, providing safe and efficient access to mining sites. The robust design of bulldozers allows them to operate in challenging environments, including steep slopes and rough terrain.

Underground, bulldozers are utilized for similar tasks, albeit on a smaller scale. They help maintain clear pathways, ensuring that other machinery can move freely and safely. Additionally, bulldozers are used to manage waste materials, keeping the mining site organized and reducing the risk of accidents.
Drills
Drills are vital in mining for both exploration and production purposes. They are used to create holes in the ground to access mineral deposits and for blasting operations. Drilling equipment varies in size and type, depending on the mining method and the material being extracted.
In exploration, core drills are used to take samples from deep within the earth. These samples are analyzed to determine the location, quality, and quantity of minerals. Core drilling is essential for making informed decisions about where to mine.
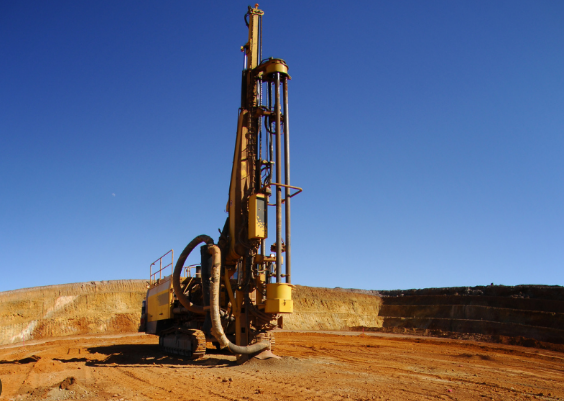
For production, blast hole drills are employed to create holes for explosives. These holes are strategically placed to ensure that the blasting process breaks apart the rock efficiently, allowing for easier extraction of minerals. Modern drilling rigs are equipped with advanced technology, such as GPS and automation, to increase accuracy and efficiency.
Loaders
Loaders are used in mining operations to load materials into haul trucks or other transporting equipment. These machines are characterized by their large buckets, which can scoop up significant amounts of material in a single pass. Loaders are crucial for moving ore, coal, and other mined materials from the extraction site to processing facilities or storage areas.
There are different types of loaders, including wheel loaders and track loaders. Wheel loaders are more versatile and can move quickly over rough terrain, making them suitable for surface mining. Track loaders, on the other hand, are better suited for soft or muddy ground, providing better traction and stability.
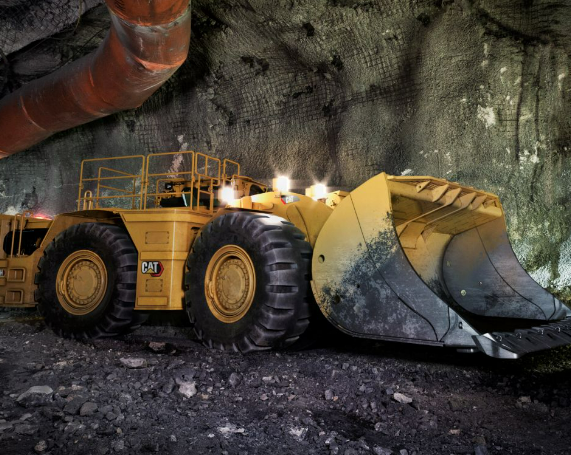
Loaders play a vital role in maintaining the flow of materials in a mining operation, ensuring that extracted resources are transported efficiently and safely. Their ability to handle large volumes of material makes them indispensable for high-production mining environments.
Haul Trucks
Haul trucks, also known as dump trucks, are the workhorses of mining operations. These massive vehicles are designed to transport large quantities of mined materials over long distances. Haul trucks are used in both surface and underground mining to move ore, coal, and waste rock from the extraction site to processing plants or disposal areas.
In surface mining, haul trucks can carry loads weighing hundreds of tons, making them one of the most efficient ways to transport large volumes of material. These trucks are built to handle the harsh conditions of mining environments, with robust frames and powerful engines.
Underground haul trucks are smaller and more maneuverable, designed to navigate narrow tunnels and tight spaces. Despite their size, they can still carry substantial loads, ensuring that materials are transported efficiently within the mine.
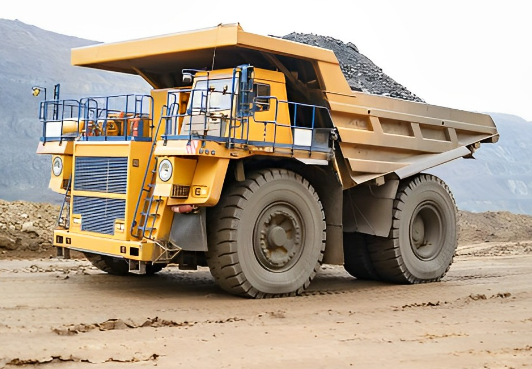
Haul trucks are equipped with advanced technology, such as automated loading and unloading systems, GPS, and real-time monitoring, to enhance productivity and safety. Their ability to move large quantities of material quickly and efficiently makes them a cornerstone of any mining operation.
Key Factors to Consider When Choosing Mining Equipment
Terrain and Geological Conditions
The terrain and geological conditions of a mining site are critical factors in determining the most suitable heavy equipment. Different types of terrain require specific machinery that can operate effectively under those conditions. For instance, rugged, uneven terrain demands equipment with high maneuverability and stability, such as tracked vehicles like bulldozers and track loaders. These machines can navigate challenging landscapes, providing better traction and control.
In contrast, relatively flat and open terrains can accommodate wheeled equipment, which tends to be faster and more efficient over longer distances. Additionally, the geological characteristics of the mining site, such as the hardness of the rock and the presence of water, influence equipment selection. Harder rocks may require more powerful drilling and blasting equipment, while areas with significant water content might need machinery with enhanced water-resistance capabilities.
Understanding the specific terrain and geological conditions helps in choosing equipment that maximizes operational efficiency and minimizes downtime caused by unsuitable machinery. Proper equipment selection ensures that the machinery can perform optimally, reducing the risk of accidents and equipment failure.
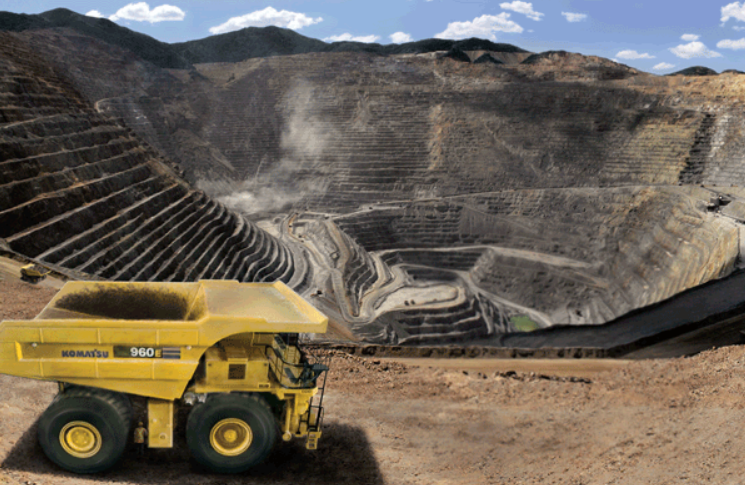
Size and Scale of Operations
The size and scale of mining operations also play a crucial role in equipment selection. Large-scale mining projects, such as open-pit mining, require heavy machinery capable of handling significant volumes of material. Excavators, haul trucks, and loaders with large capacities are essential to keep up with the high production demands.
For smaller-scale operations or underground mining, more compact and versatile equipment is often needed. Smaller excavators, narrow-body haul trucks, and agile loaders can navigate tight spaces and perform efficiently in confined environments. The scale of operations also influences the number and types of equipment required. Large-scale projects may need a fleet of machines to ensure continuous operation, while smaller projects might operate effectively with fewer, multipurpose machines.
Selecting equipment that matches the scale of the operation ensures that resources are utilized efficiently, and production targets are met without overextending the budget or underutilizing machinery.
Fuel Efficiency and Environmental Impact
Fuel efficiency and environmental impact are increasingly important considerations in mining operations. Heavy equipment can consume vast amounts of fuel, leading to significant operational costs and environmental concerns. Choosing machinery with high fuel efficiency can substantially reduce expenses and lower the carbon footprint of mining activities.
Modern mining equipment often features advanced technologies aimed at improving fuel efficiency and reducing emissions. Hybrid engines, automated systems, and energy-efficient designs help minimize fuel consumption while maintaining high performance. Additionally, equipment that produces lower emissions is crucial for complying with environmental regulations and reducing the impact on local ecosystems.
Evaluating the fuel efficiency and environmental impact of heavy equipment helps in selecting machinery that aligns with both economic and environmental goals, promoting sustainable mining practices.
Cost and Budget Constraints
Cost and budget constraints are fundamental factors in choosing mining equipment. The initial purchase price, operating costs, maintenance expenses, and potential resale value must all be considered to ensure a sound investment. While it might be tempting to opt for the cheapest option, it is essential to evaluate the total cost of ownership over the equipment’s lifespan.
High-quality machinery often comes with a higher upfront cost but offers better performance, durability, and lower long-term maintenance expenses. Investing in reliable equipment reduces the risk of frequent breakdowns, operational disruptions, and costly repairs. Additionally, considering the resale value of equipment can provide financial benefits when it’s time to upgrade or replace machinery.
Balancing cost and quality ensures that mining operations remain financially viable while maintaining high productivity and efficiency.
Technology and Automation
The integration of technology and automation in mining equipment is transforming the industry, enhancing efficiency, safety, and productivity. Modern machinery is equipped with advanced features such as GPS, real-time monitoring, automated controls, and remote operation capabilities. These technologies enable precise and efficient operations, reducing human error and increasing output.
Automated equipment can operate continuously, improving productivity and reducing downtime. For instance, autonomous haul trucks can transport materials without the need for human drivers, optimizing logistics and minimizing labor costs. Real-time monitoring systems provide valuable data on equipment performance, maintenance needs, and operational efficiency, allowing for proactive management and timely interventions.
Incorporating technology and automation in equipment selection ensures that mining operations stay competitive, leveraging the latest advancements to maximize performance and safety.
Maintenance and Support
Maintenance and support are critical considerations when choosing mining equipment. Regular maintenance is essential to keep machinery in optimal working condition, preventing unexpected breakdowns and extending the equipment’s lifespan. Choosing equipment from reputable manufacturers with robust support networks ensures access to spare parts, technical assistance, and maintenance services.
It is important to assess the availability and cost of spare parts, the ease of performing routine maintenance, and the manufacturer’s support infrastructure. Equipment with user-friendly maintenance features, such as easily accessible components and diagnostic systems, can reduce downtime and maintenance costs.
Investing in equipment with strong maintenance and support structures ensures operational continuity, minimizes disruptions, and enhances the overall efficiency and reliability of mining operations.
Key Brands and Models of Mining Equipment
Excavators
Caterpillar (CAT) 6020B: This large hydraulic mining shovel offers exceptional digging power and high production rates. It features a durable design and advanced technology for optimal performance.
Komatsu PC8000-6: Known for its reliability and efficiency, this excavator is designed for heavy-duty mining applications. It offers a spacious cab, user-friendly controls, and robust hydraulics.
Hitachi EX5600-6: This model is highly efficient in material handling and offers excellent operator comfort and safety features. It is well-suited for large-scale mining projects.
Bulldozers
Caterpillar D11: One of the largest bulldozers in the world, the CAT D11 is known for its exceptional pushing power and durability. It features advanced technologies like automated blade assist and terrain monitoring.
Komatsu D475A-8: This bulldozer offers high productivity and fuel efficiency. It features a powerful engine, comfortable operator cab, and innovative hydraulic systems.
John Deere 1050K: Known for its strength and reliability, this model provides excellent control and precision. It is equipped with advanced telematics for real-time monitoring and maintenance management.
Drills
Sandvik DR416i: This rotary blasthole drill is known for its efficiency and reliability in large-scale mining operations. It features advanced automation and a powerful rotary head.
Atlas Copco Pit Viper 351: Designed for open-pit mining, this drill offers high penetration rates and robust construction. It is equipped with GPS and telematics for precise drilling.
Epiroc DM-M3: This model is renowned for its versatility and efficiency in various drilling applications. It features a modular design and advanced control systems for optimal performance.
Loaders
Caterpillar 994K: This large wheel loader is known for its durability and high load capacity. It features advanced hydraulics and a comfortable operator cabin.
Komatsu WA1200-6: Renowned for its powerful performance and efficiency, this loader offers a robust design and advanced technologies for enhanced productivity.
Volvo L350H: This model is known for its fuel efficiency and operator comfort. It features advanced telematics for real-time monitoring and maintenance management.
Haul Trucks
Caterpillar 797F: One of the largest haul trucks in the world, the CAT 797F offers exceptional load capacity and durability. It features advanced technologies like autonomous hauling and real-time monitoring.
Komatsu 980E-4: Known for its high payload capacity and fuel efficiency, this haul truck is designed for large-scale mining operations. It features a comfortable operator cabin and advanced control systems.
Belaz 75710: The world’s largest haul truck, the Belaz 75710 offers unparalleled load capacity and robust construction. It is equipped with advanced safety features and automation technologies.
Conclusion
Choosing the best heavy equipment for mining is a critical decision that significantly impacts the efficiency, safety, and profitability of mining operations. Understanding the specific requirements of your mining site, including terrain, geological conditions, and the scale of operations, is essential in making informed equipment choices. Each type of equipment, from excavators and bulldozers to drills, loaders, and haul trucks, plays a unique and vital role in the mining process.
At HOLIGHT Industrial Group, we specialize in delivering high-quality, reliable second-hand excavators, loader, roller and bulldozer from top brands. Based in China, we focus on providing affordable and sustainable solutions for your construction needs.