Maintaining excavator tracks is crucial for ensuring the efficient and safe operation of your equipment. Excavator tracks bear the brunt of harsh terrains, heavy loads, and constant movement, making them susceptible to wear and tear. Regular maintenance not only keeps your excavator running smoothly but also brings several key benefits:
Improved Performance: Well-maintained tracks provide better traction and stability, leading to smoother and more efficient operation. This is essential for completing tasks effectively and on time.
Extended Lifespan: Regular upkeep can significantly extend the lifespan of your tracks. By addressing minor issues early, you prevent them from developing into major problems that could require costly replacements.
Cost Savings: Preventative maintenance helps avoid unexpected breakdowns and expensive repairs. Investing a little time and effort in regular maintenance can save you a substantial amount of money in the long run.
In this blog post, we’ll cover the essential steps and best practices for maintaining excavator tracks, ensuring they remain in optimal condition for as long as possible.
Types of Excavator Tracks
To maintain your excavator tracks effectively, it’s important to understand their types and components. Excavator tracks come in two main types: rubber and steel. Each type has its advantages and is suited for different working conditions.
Advantages of Rubber Tracks:
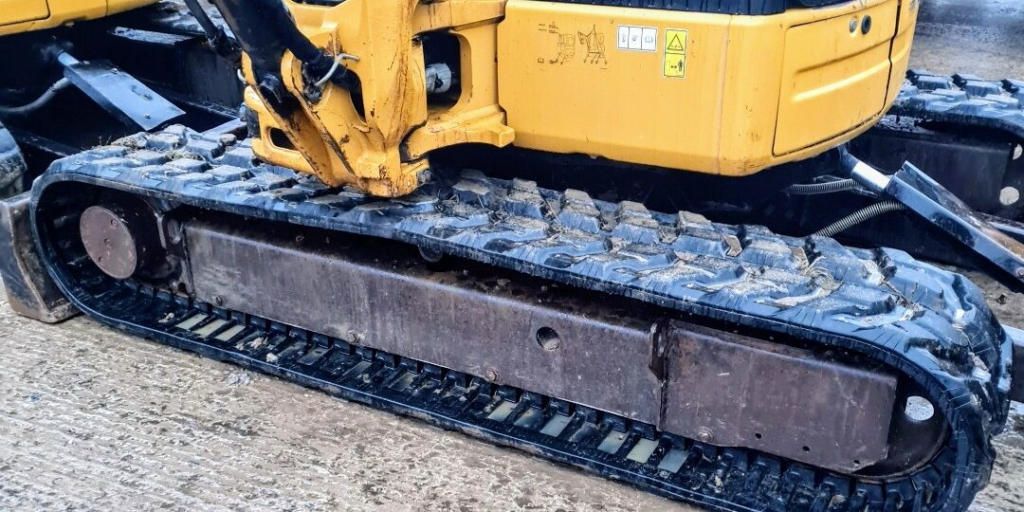
Flexibility and Traction: Rubber tracks are more flexible, providing excellent traction on various surfaces, including paved roads and delicate grounds like grass or dirt.
Reduced Vibration: They offer smoother operation with less vibration, making them ideal for urban areas and landscaping projects.
Surface Protection: Rubber tracks are less likely to damage surfaces, making them suitable for work in residential or sensitive areas.
Advantages of Steel Tracks:
Durability and Strength: Steel tracks are highly durable and can withstand harsh conditions and rough terrains, including rocky and muddy environments.
Heavy-Duty Performance: They provide superior performance for heavy-duty tasks and long-term projects, especially in construction and mining.
Longevity: Steel tracks typically have a longer lifespan compared to rubber tracks, making them a preferred choice for rigorous applications.
Key Components of Excavator Tracks
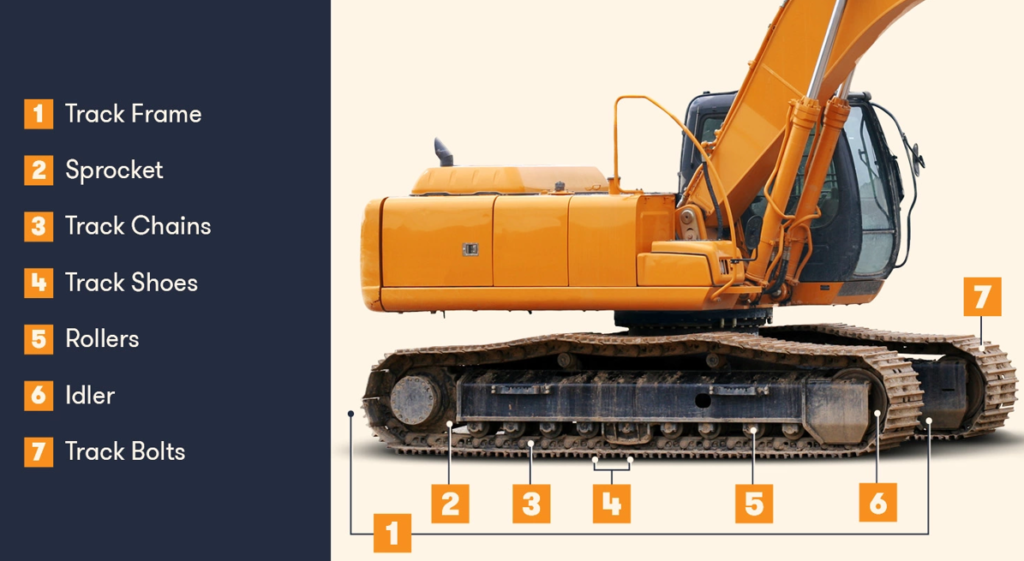
Track Chains: These are the main links that form the track and provide the foundation for the excavator’s movement.
Track Shoes: Attached to the track chains, these provide the contact surface with the ground. Rubber or steel pads can be added depending on the type of track.
Rollers: There are two types of rollers – bottom rollers and top rollers. Bottom rollers support the track and allow it to move smoothly over the surface, while top rollers keep the track aligned and in place.
Idlers: These are located at the front of the track frame and help guide and tension the track.
Sprockets: Positioned at the rear, sprockets drive the track by engaging with the track links.
Track Tensioner: This component helps maintain the correct tension in the track to ensure proper alignment and prevent de-tracking.
Understanding these types and components will help you perform more effective maintenance and keep your excavator tracks in optimal condition.
Daily Inspection Routine for Excavator Tracks
A daily inspection routine is crucial for maintaining your excavator tracks and ensuring they perform optimally. Regular checks help identify issues early, preventing costly repairs and downtime. Here’s a step-by-step guide to an effective daily inspection routine:
1.Visual Inspection Tips:
Clean the Tracks: Before starting your inspection, remove dirt, mud, and debris from the tracks. This allows you to see potential problems clearly.
Look for Cracks and Damage: Examine the track shoes for cracks, breaks, or any visible damage. Pay close attention to the edges and corners.
Inspect Rollers and Idlers: Check the rollers and idlers for signs of wear or damage. Ensure they are turning freely and are not cracked or broken.
Examine Sprockets: Look at the sprockets for wear on the teeth. Worn teeth can cause the tracks to slip and reduce efficiency.
Check Track Alignment: Ensure the tracks are properly aligned. Misalignment can lead to uneven wear and reduce track life.
2.Checking for Wear and Tear:
Track Tension: Proper track tension is essential for optimal performance. Tracks that are too loose can de-track, while overly tight tracks can cause excessive wear. Refer to your manufacturer’s guidelines for the correct tension specifications.
Track Links and Pins: Inspect the track links and pins for signs of wear. Worn pins and links can cause the track to stretch and reduce its effectiveness.
Track Shoes: Check the track shoes for wear patterns. Uneven wear can indicate alignment issues or improper track tension.
3.Identifying Common Issues:
Loose Bolts: Check all bolts on the track assembly, including those on the track shoes, sprockets, and rollers. Tighten any loose bolts to prevent parts from detaching during operation.
Cracked or Broken Components: Look for any cracked or broken components, such as rollers, idlers, and track shoes. Replace damaged parts promptly to avoid further damage.
Leaking Fluids: Inspect the area around the tracks for any signs of leaking fluids, which can indicate issues with the hydraulic system or lubricants.
Unusual Noises: Listen for unusual noises when the excavator is in operation. Grinding, squeaking, or clanking sounds can indicate problems with the track components.
By following this daily inspection routine, you can catch potential problems early and keep your excavator tracks in top condition, ensuring smooth operation and extending the life of your equipment.
Cleaning and Lubrication of Excavator Tracks
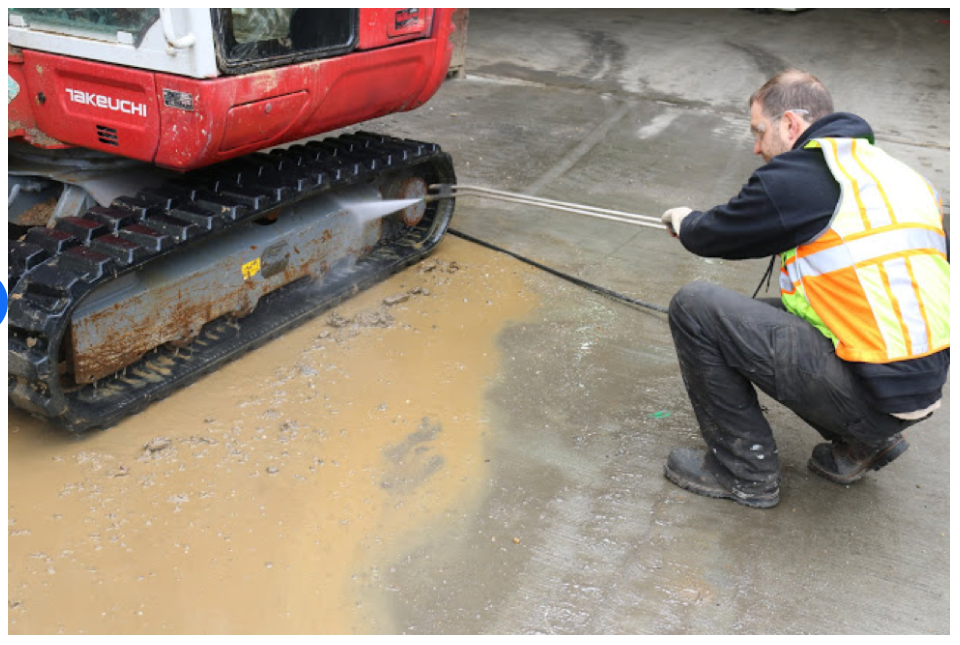
Maintaining clean and properly lubricated excavator tracks is vital for ensuring optimal performance and longevity. Regular cleaning and lubrication prevent the buildup of debris and reduce wear and tear on track components. Here’s how to keep your tracks in top condition:
Importance of Keeping Tracks Clean:
Preventing Wear and Tear: Dirt, mud, and debris can accelerate wear on track components. Regular cleaning removes abrasive materials that can damage the tracks and undercarriage.
Avoiding Track De-tracking: Built-up debris can cause tracks to become misaligned or de-track, leading to operational downtime and potential damage.
Improving Performance: Clean tracks ensure smoother operation, better traction, and improved fuel efficiency.
Lubrication Tips for Track Components:
Track Pins and Bushings: Lubricate track pins and bushings regularly to reduce friction and wear. Use high-quality grease recommended by the excavator manufacturer.
Rollers and Idlers: Ensure that rollers and idlers are adequately lubricated. Check grease fittings and apply grease as specified in the maintenance manual.
Sprockets: Lubricate sprockets to minimize wear on the teeth and ensure smooth track movement. Inspect for signs of wear and apply grease as needed.
Track Tensioner: Keep the track tensioner well-lubricated to maintain proper track tension and alignment. Regularly check the tensioner for leaks and proper operation.
By keeping your excavator tracks clean and well-lubricated, you can enhance their performance, extend their lifespan, and reduce the risk of unexpected breakdowns. Regular cleaning and lubrication are simple yet effective steps in your maintenance routine that yield significant benefits in the long run.
Regular Maintenance Tasks
Regular maintenance is essential to keep your excavator tracks in optimal condition. By scheduling inspections, replacing worn-out components, and recognizing the signs that tracks need replacement, you can ensure your equipment operates efficiently and safely.
Operating Tips to Extend Track Life
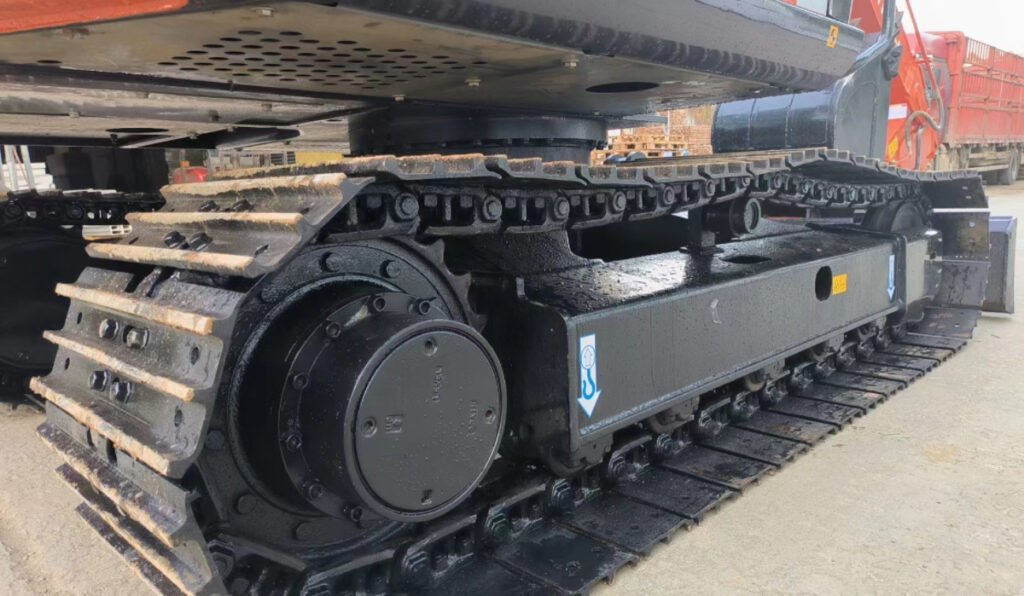
Proper operating techniques can significantly extend the lifespan of your excavator tracks. By following best practices for different terrains, avoiding sharp turns and excessive speed, and minimizing undercarriage damage, you can ensure your tracks last longer and perform optimally.
Best Practices for Operating on Different Terrains:
1.Soft Ground (Mud, Sand, and Snow):
Reduce Speed: Move slowly to prevent tracks from digging too deeply into soft ground.
Avoid Spinning: Avoid spinning the tracks, as this can cause them to sink or become stuck.
Wide Turns: Make wide turns to reduce stress on the tracks and undercarriage.
2.Hard Ground (Gravel, Rocks, and Asphalt):
Moderate Speed: Operate at a moderate speed to reduce wear on the track shoes and minimize impact on the undercarriage.
Track Cleaning: Regularly clean tracks to remove abrasive materials that can cause wear.
Avoid Sharp Objects: Steer clear of sharp objects and large rocks that can damage the tracks.
3.Inclined or Uneven Terrain:
Approach Angles: Approach slopes at an angle rather than head-on to distribute weight evenly.
Avoid Side Slopes: Minimize operation on steep side slopes to prevent track slippage and uneven wear.
Smooth Transitions: Make smooth transitions between different terrain levels to reduce impact on the tracks.
Avoiding Sharp Turns and Excessive Speed:
Wide Turns: Always make wide, gradual turns instead of sharp ones. Sharp turns can cause the tracks to de-track and increase wear on the undercarriage components.
Controlled Speed: Operate at a controlled speed that matches the terrain conditions. High speeds can cause increased wear and tear on the tracks and undercarriage.
Gentle Maneuvering: Be gentle with the controls to prevent sudden movements that can strain the tracks and other components.
Minimizing Undercarriage Damage:
Regular Cleaning: Clean the undercarriage regularly to remove dirt, mud, and debris. Accumulated debris can cause accelerated wear and hinder track performance.
Avoid Obstructions: Steer clear of obstacles like large rocks, stumps, and debris that can damage the undercarriage and tracks.
Track Alignment: Ensure the tracks are properly aligned and tensioned. Misalignment can cause uneven wear and increase the risk of de-tracking.
Proper Lubrication: Keep all moving parts of the undercarriage well-lubricated to reduce friction and wear.
Even Weight Distribution: Avoid carrying loads unevenly, as this can cause one side of the tracks to wear faster than the other.
By incorporating these operating tips into your daily routine, you can significantly extend the life of your excavator tracks. Proper handling and mindful operation not only enhance track longevity but also improve overall machine performance and safety.
Conclusion
Regular maintenance is not just about preventing issues but also about optimizing your excavator’s performance and extending its lifespan. By following a consistent maintenance schedule, you can avoid unexpected breakdowns, reduce operational costs, and maintain a high level of productivity.
In conclusion, investing time and effort in maintaining your excavator tracks pays off significantly. It leads to improved machine performance, greater safety, and substantial cost savings in the long run. Keep your tracks in optimal condition to ensure your excavator remains a reliable and efficient tool for all your projects.